Our Services

Reliable Cable Solutions
At Kato Cable, we offer comprehensive services to support every stage of your wire harness and electronic assembly needs. From design and prototyping to manufacturing and quality assurance, our expert team ensures precision, reliability, and efficiency. With a commitment to innovation and customer collaboration, we deliver solutions that meet the highest industry standards.
Over Molding

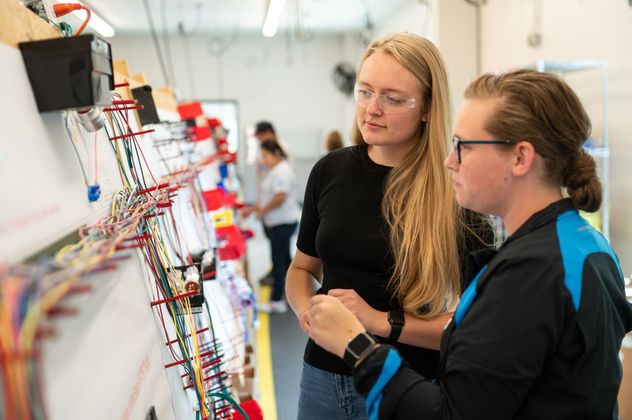
Process Control & Engineering Control Services
Process Control
Precision and consistency are at the heart of every custom cable solution. Our Process Control strategies ensure each assembly meets exact specifications, from initial concept to final production. Through rigorous quality checks, standardized procedures, and real-time monitoring, we optimize efficiency while maintaining the highest level of reliability.
Engineering Control
From concept to completion, Engineering Control ensures every design is optimized for functionality, manufacturability, and long-term performance. Our expert team evaluates form, fit, and function, applying industry best practices, testing protocols, and innovative solutions to deliver high-quality, cost-effective cable and harness assemblies.
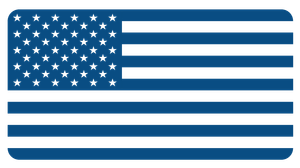
Our Products are Proudly Made in the USA
The Kato Cable Advantage
It is a holistic approach to looking at the value that you bring to your customers, employees and community. Our customers relate directly to our responsiveness, our engineering value, our investments that we have made into efficiencies and automation, as well as the key metrics of industry leading Quality and On Time Delivery. Our employees relate to a sense of inclusion, an appreciation and value to feedback, and the philosophy of making improvements every day. Our community relates to our growth and volunteerism and leadership that we strive for in our region. Together these attributes and values truly deliver the Kato Cable Advantage!
Quality & Reliability
Delivering precision-engineered wire harnesses, cable assemblies, and electro-mechanical assemblies that meet the highest industry standards.
Innovation
Continuously improving processes and technologies to provide cutting-edge solutions for diverse industries.
Customer Commitment
Building strong partnerships through collaboration, responsiveness, and tailored solutions.
Our Certifications
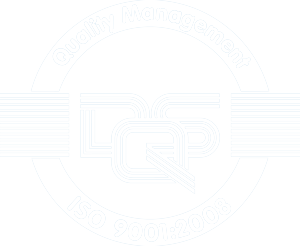
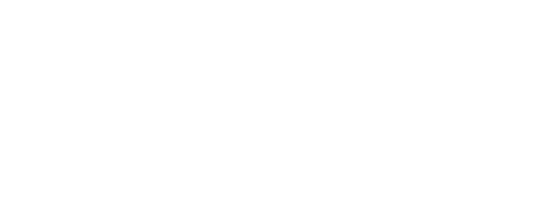
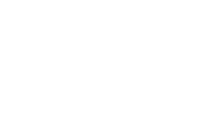
FAQs
What is a Komax Zeta, and how does it benefit cable assembly?
The Komax Zeta is a high-performance wire processing machine that automates the measuring, marking, cutting, stripping, and crimping of wires. It helps improve efficiency, precision, and scalability, making it ideal for higher-volume and complex cable assembly production.
What is your standard lead time?
Our standard lead time for a first-time build (aka NPI) is 10-12 weeks. After that, 6-8 weeks is standard. This can vary based on market conditions and material availability.
What's the difference between UL1007 and 1015 wire?
UL1007 wire has a lower temperature rating (up to 80°C) and is typically used for low-voltage, general-purpose applications like electronics and control panels. UL1015 wire, with a higher temperature rating (up to 105°C), is designed for more demanding environments such as automotive and industrial applications, where heat resistance and durability are crucial.
What are the main differences between GXL and TXL wires?
GXL and TXL wires are both types of automotive-grade wire, but GXL has thicker insulation and is designed for higher-temperature environments, while TXL wire has a thinner insulation, making it more flexible and suitable for tight spaces. Both are commonly used in wire harnesses for automotive applications.
How large is your facility?
We currently have 63,000 square feet of manufacturing floor space, with room for future expansion.
What is a wire harness?
A wire harness is a bundle of electrical wires or cables that are grouped together, organized, and often secured with protective coverings like tape or plastic. It is designed to simplify the installation process, reduce the risk of electrical shorts, and ensure that electrical connections are easily managed. Wire harnesses are commonly used in vehicles, machinery, and electronics to route power and signals between different components.
Why change my design from striped wires to solid colors?
We currently have all solid colors integrated into our Komax Zeta machines. If your design uses solid colors, we can significantly reduce setup time for our automation equipment, resulting in both time and cost savings. If you're concerned about distinguishing between wires, we offer custom printing and labeling options to meet your needs.
What is ISO 9001:2015?
ISO 9001:2015 is an international standard for quality management systems (QMS). It provides a framework for organizations to ensure they meet customer needs and regulatory requirements while continuously improving processes. The 2015 version emphasizes risk-based thinking, leadership involvement, and a focus on customer satisfaction, helping businesses improve efficiency, consistency, and overall performance. Organizations that are ISO 9001:2015 certified demonstrate their commitment to quality and continuous improvement.
What is your average quote turnaround time?
Our average quote turnaround time is 2 weeks.
Client Testimonials
Ryan B.
Angela W.
Aaron R.
Jim K.
Mark M.
"Kato Cable is a leader in the market for wire & cable assemblies. They have a first-class team that is dedicated to the continuous improvement and high quality. They lead the way in automation and efficiency in production. The team at Kato Cable is devoted, hardworking, and a joy to work with."
"We value strong partnerships, and Kato Cable has consistently proven to be a trusted and reliable supplier. Their expertise in custom cable assembly and harness manufacturing ensures reliable products that enhance our operations. The Kato Cable team is knowledgeable, responsive, and always a pleasure to work with, demonstrating a true collaborative spirit in every project. We truly value our partnership and look forward to continued success together."
"Partnering with Kato Cable was an easy decision; the team supports communication at all levels resulting in quality assembled enclosures. Kato Cables culture and values aligned with our Upscale philosophy – build quality products, relationships, and understand customer needs. The collaborative spirit of the Kato Cable team has been instrumental in driving our projects forward. Working with Kato Cable has sincerely been a pleasure."
"A great partnership that mirrors a close friendship."
“As a trusted distributor in the industry, we have had the pleasure of working with Kato Cable LLC for several years, and we can confidently say that their products and service are second to none. Kato Cable consistently delivers high-quality products while meeting demanding standards and specifications. Kato Cable has strategic programs in place for product availability and timely delivery to ensure that they can meet their end customers' needs without delay. The customer service team at Kato Cable is exceptional—always responsive, knowledgeable, and willing to go the extra mile. They provide comprehensive technical support, focusing on the end customer’s needs, which is invaluable when working with complex cable solutions. Additionally, their competitive pricing and commitment to innovation make them a preferred partner in our industry. Working with Kato Cable LLC has been a rewarding experience, and we highly recommend their products and services to any business looking for a reliable, quality-driven cable supplier."
Stay Connected with our Blog

Services Contact Us
We will get back to you as soon as possible.
Oops, there was an error sending your message. Please try again later.
Looking for Support?
Our team is here to help. Whether you’re looking for a custom solution or need support with an existing project, we’re just a message away. Reach out today, and let’s find the right solution for you.